Cad Jewelry Design Biography
Source(google.com.pk)Jason Busch is an established designer in North Texas. For over two decades, Jason has been creating cutting edge graphic design and full marketing development for businesses of all types and sizes. While pursuing a full time position at Brown & Partners in pre-press production, he collaborated with some of the most skillful print designers and copywriters in Dallas, producing luxurious jewelry catalogs, bill boards and other marketing ads for Tiffany & Co., Rolex, Baily Banks & Biddle, Zales, Lux Bond & Green, and many others.
After 7 years of designing and developing print and web professionally, Jason discovered the power of 3D modeling and 3D Printing (CAD/CAM). The implementation of CAD/CAM technology to the jewelry industry was at its birth. Working with engineers and fellow designers from all over the world, Jason has been successfully and consistently applying this technology to create some of the world's most elegant fine jewelry design with unmatched manufacturing precision.
Working exclusively with local top master bench jewelers and established diamond manufactures/importers, Jason is currently providing commited wholesale Jewelry Design, Manufacturing, Marketing and CAD/CAM Consulting services and training. Please feel free to contact Jason Busch directly for inquiries or appointment requests.
Here's how to create a classic Diamond engagement ring from start to finish. This custom ring is made in Platinum and has one hundred small Diamonds set in the mounting. This particular style mounting uses a method known as bead setting- there are four tiny metal beads that hold each small stone in place. I'll show you how the design begins with a CAD model and walk you through the entire creation process step by step. If you ever wondered how jewelry like this is made or you're an aspiring jeweler looking to expand your stone setting skills then this is for you!
Picture of Tools
A lot of tools were used in the creation of this ring. I'll give a general overview and then explain how all the tools are used in greater detail in the relevant sections. This isn't meant to be a complete list of all the tools used in jewelry making but it does represent all of the tools used in the creation of this particular ring.
1.) You need a solid workbench. This is where the magic happens! The vast majority of work is done at the jewelers bench. Every jeweler has their own preferences in regards to how their bench is set up and in the 15 years I've been working as a jeweler I've certainly developed my own sense of what works and what doesn't. That doesn't mean there isn't a different/better way of doing things- this is just my own personal preference. A jeweler's bench should have a thick sturdy top (it'll get hammered on a lot) and it should have a large metal lined pan to catch metal filings/scrap. I keep most of my larger tools like large hammers, files, ring mandrel, sanding sticks and my saw in this pan so I can quickly grab them.
2.) Good lighting is a must. Making jewelry is hard on your eyes so make sure you have lots of light at your work space. I use a magnifying ring light and I've found it to have nice even light. The magnification isn't very strong but it's nice to be able to drop it down in front of you to get a better view of what you're working on.
3.) When doing exacting detail work good magnification is really important. I wore magnifiers for years before getting a bench mounted stereo zoom microscope and I can tell you there is no comparison. The microscope offers much better magnification and field of view as well as a greater working distance, which is necessary when doing detailed engraving and stone setting. The microscope is mounted on a stand that allows it to be positioned wherever I want. When looking for a microscope you want one that is designed for engraving work. The Omano microscopes are a really good buy too. Whatever scope you get be sure to get a LED ring lamp for it and make sure it has a .5X Barlow lens. The Barlow lens will increase the focal distance so you have room to move your hands under the scope while engraving and stone setting.
4.) Rotary tools. I probably use these more than any other bench tool. Rotary tools are used for drilling, grinding and sanding. I have two Foredom flexshaft motors- one with a quick change handpiece and another with a #30 handpiece. The quick change handpieces are really nice for stone setting since you can change burs really fast. The #30 handpiece is great for using drill bits, large sanding rolls and large rotary burs. The Foredom flex shaft motors last forever- mine are over 15 years old. The #30 handpiece will also last forever. I manage to wear out the quick change handpieces every 1 1/2 to 2 years. I recently started using a NSK Evolution EMax micromotor rotary tool and it's the cat's pajamas. It is simply the finest rotary tool I've ever used and they're known for being extremely robust. The big benefit of micromotor rotary tools is the motor is in the handpiece so you're not fighting the tension of a flex shaft drive cable- it's a pretty big deal when you're doing delicate work and stone setting.
Cad Jewelry Design Jewelry Desgin Sketches Ideas 2014 Neclkace Ring Earringes Gallery Bangles Software Drawing Images Photos Wallpapers

Cad Jewelry Design Jewelry Desgin Sketches Ideas 2014 Neclkace Ring Earringes Gallery Bangles Software Drawing Images Photos Wallpapers

Cad Jewelry Design Jewelry Desgin Sketches Ideas 2014 Neclkace Ring Earringes Gallery Bangles Software Drawing Images Photos Wallpapers
Cad Jewelry Design Jewelry Desgin Sketches Ideas 2014 Neclkace Ring Earringes Gallery Bangles Software Drawing Images Photos Wallpapers
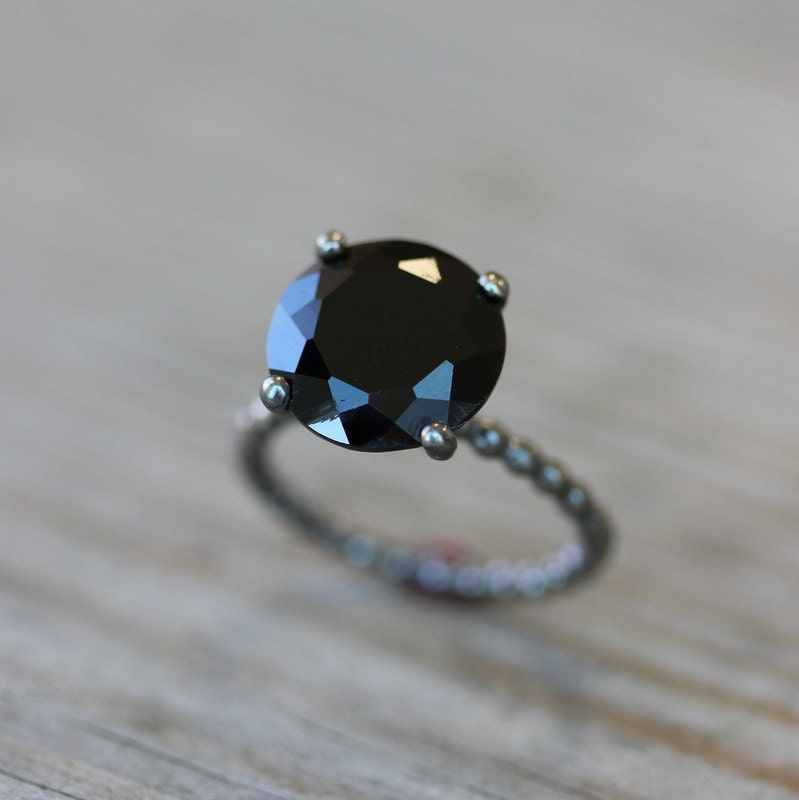
Cad Jewelry Design Jewelry Desgin Sketches Ideas 2014 Neclkace Ring Earringes Gallery Bangles Software Drawing Images Photos Wallpapers
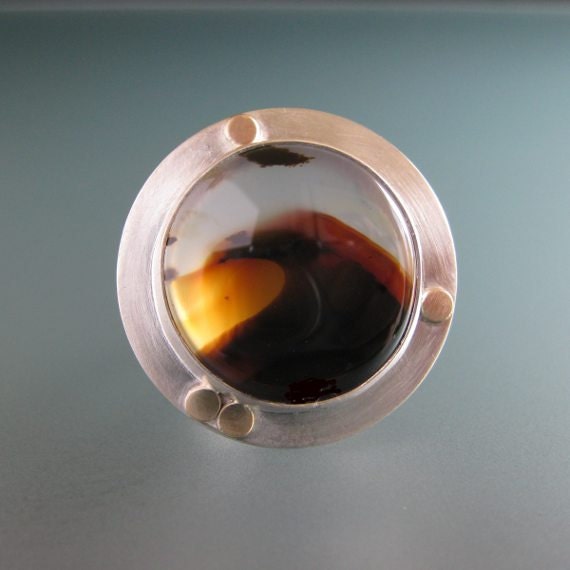
Cad Jewelry Design Jewelry Desgin Sketches Ideas 2014 Neclkace Ring Earringes Gallery Bangles Software Drawing Images Photos Wallpapers
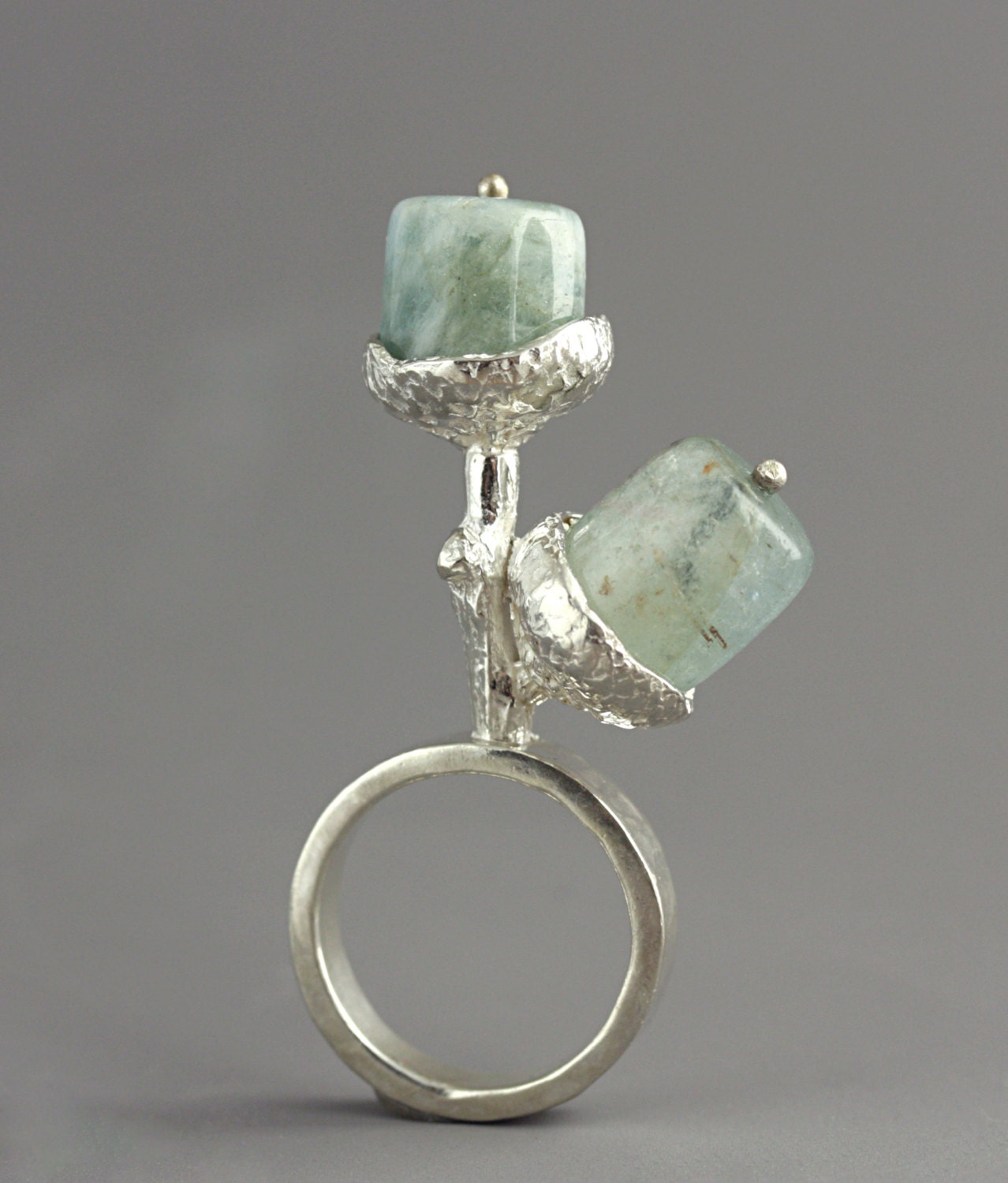
Cad Jewelry Design Jewelry Desgin Sketches Ideas 2014 Neclkace Ring Earringes Gallery Bangles Software Drawing Images Photos Wallpapers
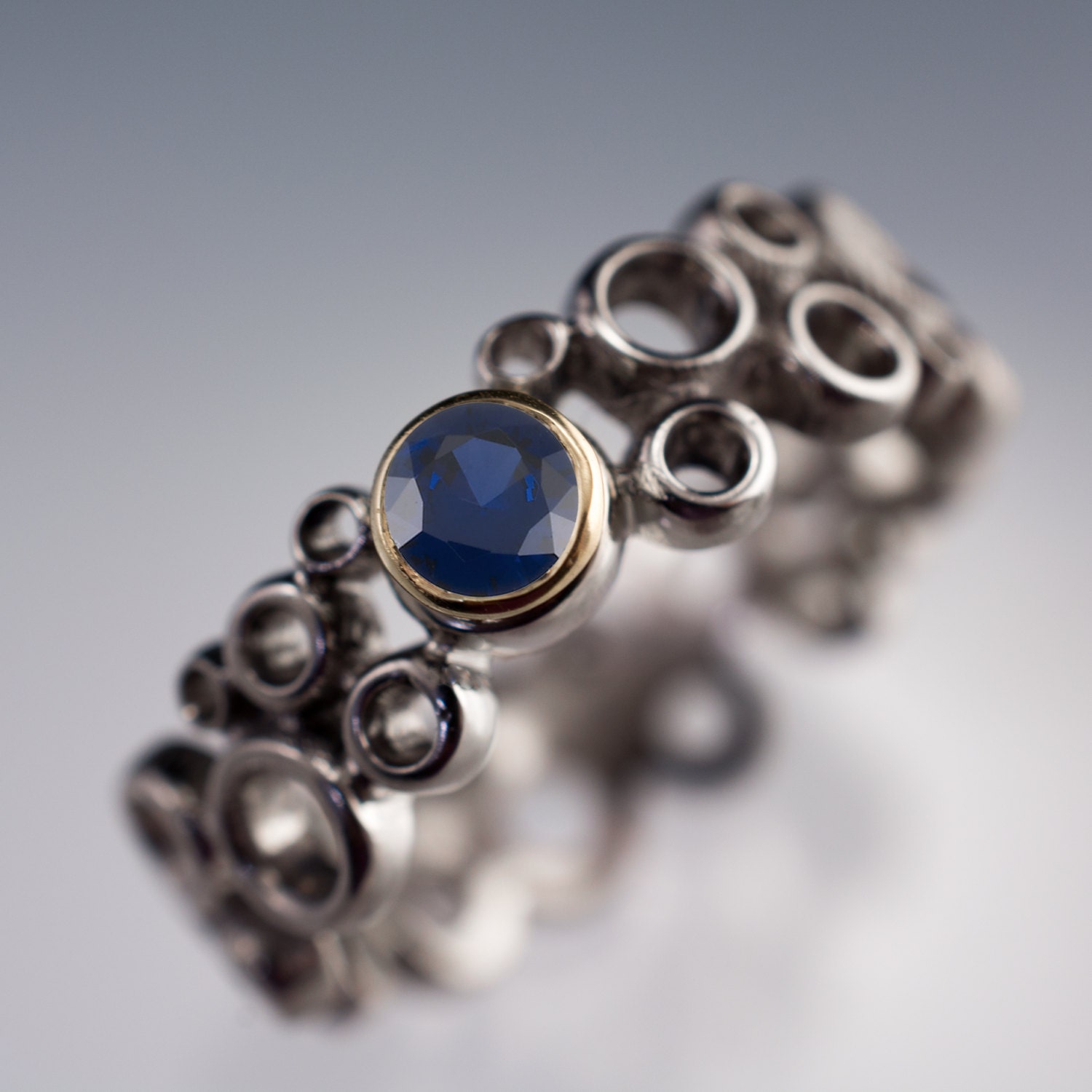
Cad Jewelry Design Jewelry Desgin Sketches Ideas 2014 Neclkace Ring Earringes Gallery Bangles Software Drawing Images Photos Wallpapers
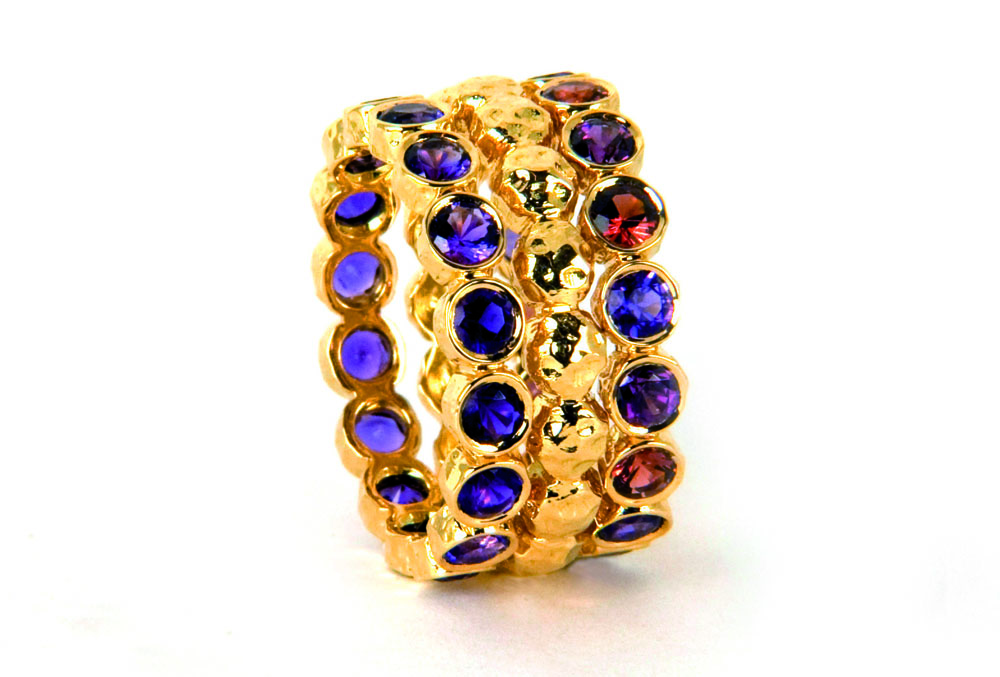
Cad Jewelry Design Jewelry Desgin Sketches Ideas 2014 Neclkace Ring Earringes Gallery Bangles Software Drawing Images Photos Wallpapers
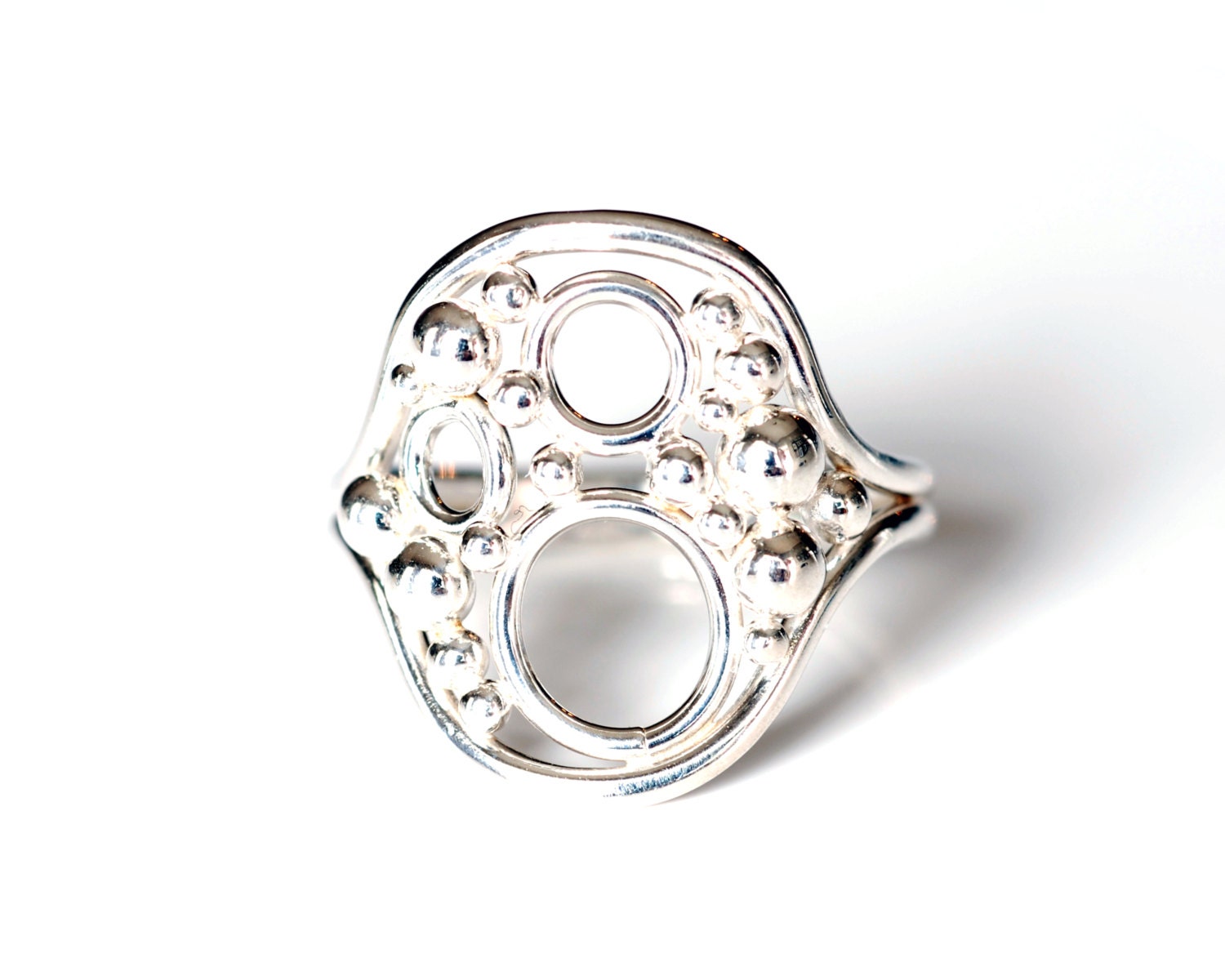
Cad Jewelry Design Jewelry Desgin Sketches Ideas 2014 Neclkace Ring Earringes Gallery Bangles Software Drawing Images Photos Wallpapers
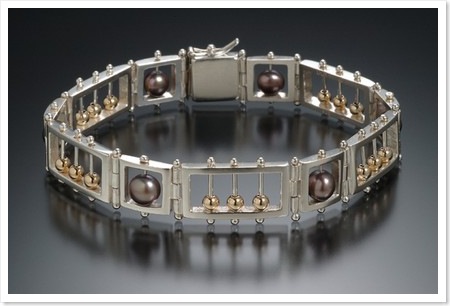
No comments:
Post a Comment