Iearn Jewelry Design Biography
Source (goohle.com.pk )I am a native of New Castle, PA where I was lucky enough to have had a great high school art program (as well as teachers!) and had the opportunity to learn jewelry making for four years. I attended the University of Pittsburgh and received a bachelor’s degree in Studio Arts & Fine Arts and continue jewelry casting at the Pittsburgh Center for the Arts.
Founded in January 2007, "On The Rocks Designs" focuses on creating one-of-a-kind, art jewelry. The name was inspired when I lamented changing my name after I got married. So when I heard the commercial for the liqueur "Disaronno" on the rocks, it sounded so similar to my maiden name, Lisa Wrona, I was inspired. At that point my business, "On The Rocks," was born and pays tribute to the artistic heritage of my family's talents and namesake. Each unique piece is named after a classic cocktail. I experiment with enameling, metal fabrication, and beading, but especially enjoy the fluidity and variety of techniques allowed by Lost Wax Casting to create unique designs which are not typical of metal, and making each piece as individual and one-of-a-kind as the person wearing it.
My primary method of creating one-of-a-kind art jewelry designs is through Lost Wax Casting. During the design phase, the interplay of melting wax and the refinement of the model is a “stream of consciousness” process in which I let the wax lead me to a design. While in this stream of consciousness, an organic flow of “mental” shapes and forms are extracted and then controlled through carving and melting the wax. The shapes that appear are a result of an emotional state or mood —the wax serving as the outlet which sets them free.
On The Rocks Designs brings a decadent and unconventional style to accessories, with one-of-a-kind jewelry in cast sterling, enamel, fabrication and innovative beading.
As an artist, it was difficult to choose just one medium and stick with it, but I seem to have an addiction to silver, shiny & unique items! Fortunately, making jewelry allows me to enjoy three of my favorite mediums: Lost Wax Casting, photography, & graphic design. I also love designing new displays as much as making jewelry. As an eco-conscious designer, cast sterling items include 40% recycled sterling silver and all enamels used are lead-free. I also enjoy the challenge of re-purposing scraps and using recycled materials, so the displays are often made of sustainable materials, leftover products from other projects, or discontinued store samples.
Making your own jewelry findings from wire is not only easy but also gives your finished jewelry a personal touch. In addition to making your own jump rings, head pins and eye pins, you can create beautiful wire clasps and earring findings using basic wire jewelry making tools.
To make beautiful wire jewelry and wire jewelry findings, you only need to know a few basic techniques such as wrapped loops, flush cutting and opening jump rings. Once you've learned and practiced these wire jewelry making techniques, you'll be able to create a wide range of styles of handmade wire jewelry.
Wire Jewelry Basics
wire-jewelry .
Learn all about the basic tools needed to create your own wire jewelry.
Shop Wire Jewelry Making
Products
Wire Jewelry Making Projects Wire Jewelry Making Projects
Wire Jewelry Making Books and eBooks Wire Jewelry Making Books and eBooks
Wire Jewelry Making Videos and DVDs Wire Jewelry Making Videos and DVDs
Wire Jewelry Making Collection CDs Wire Jewelry Making Collection CDs
Wire Jewelry Making eMags Wire Jewelry Making eMags
Wire Jewelry Making Magazines Wire Jewelry Making Magazines
Wire Gauge Wire comes in different gauges, or thicknesses, which are noted as numbers. When figuring out wire thickness, a smaller number is assigned to a thicker wire. A 16 gauge wire will be much thicker than a 28 gauge wire.
Wire Hardness Wire also comes in different hardness. This refers to the ease with which the wire can be shaped and its ability to retain this shape under stress. A dead-soft wire is easily bent with your fingers and can be manipulated after shaping. A full-hard wire usually requires the help of jewelry making pliers and will retain its shape under stress. You can always work-harden your wire components and findings by tumbling them after you've finished them.
Wire Shape Wire comes in three basic shapes: round, half-round and square. You can tell which shape of wire you are using by looking at a cross-section of wire. A round wire will look like a circle. Half-round will resemble a half moon. And square wire will resemble a square. You can also find twisted wire that has lovely little grooves worked into it and wire with floral and geometric patterns.
Tools for Working With Wire
wire-jewelry .
You can use the jewelry pliers you already have to combine beadweaving with wire to create stunning jewelry!
The basic tools that you need to get started making wire jewelry are easy to find. In general, it is always better to buy the best wire working tools that you can afford. Quality tools will be easier on your hands and will last longer. And tools that feel better in your hands when you're working with them will make your time spent making wire jewelry more enjoyable!
Wire Cutters Also known as flush cutters, these are required for making clean cuts of different sizes and types of wire. Most cutters have a flat side for smooth cuts and an angled side for making sharper cuts.
Round-Nose Pliers Round-nose pliers are perfect for creating even, round loops. The jaws of these wire working pliers should be smooth and come to a tapered point.
Flat-Nose Pliers These pliers are used for gripping wire while working it into shape. The jaws of flat-nose pliers are flat and broad and come to a somewhat tapered point. These pliers are also handy for pulling Viking knit chain through a draw plate.
Chain-Nose Pliers These wire working pliers are a combination of round-nose and flat-nose pliers. The jaws are rounded on the outside and flat on the inside, coming to a tapered point. These pliers are helpful for crimping down the ends of wrapped wire and for grasping wire in tight spaces.
Wire Straighteners Also called wire smoothers, these are broad, nylon-jawed pliers that are used to smooth or straighten wire that has come off of a spool.
Tools for Making Wire Jewelry Findings
. wire-jewelry
. Use basic wire techniques to make custom jewelry clasps like these.
If you want to make your own wire jewelry findings (and why not?) you'll need a few additional tools.
Wire Hammer A nylon wire hammer is very useful for flattening wire without marring the surface. Hammering your finished wire components is also a good way to work-harden them and prevent them from losing their shape.
Small Anvil or Steel Bench Block These tools provide a firm surface for hammering and work-hardening your wire jewelry findings and components. You can also find bench blocks made of nylon and with a rubber base for absorbing shock and noise.
Mandrels A mandrel is used for making consistent, evenly-sized loops in your wire that you can nip off into perfect jump rings. If you don't want to purchase a wire jewelry making mandrel, you can just use a smooth knitting needle, pencil, or wooden dowel.
Knitting and Crocheting with Wire
Knitting and crocheting with wire gives you beautiful and unique jewelry and home décor items. All that's needed in addition to your basic wire jewelry-making tools is a set of knitting needles or a crochet hook.
Basic crochet stitches like chain stitch, single crochet and double crochet can be used with fine wire to create lightweight and comfortable jewelry. The addition of beads to your wire crochet projects will add extra sparkle!
Knitting with wire also uses basic knitting techniques and fine wire. The only difference when knitting with wire is that you'll have to work with a very loose tension because the wire won't stretch like yarns or fibers.
Viking knit is an ancient and popular way to make smooth wire chains for necklaces and bracelets. Viking knit chains can be started on either a simple Allen (or hex) wrench or on a commercial mandrel designed specifically for doing Viking knit.
7 Tips for Working with Wire
1. Practice on craft wire. Perfect your wire jewelry-making techniques and skills by using low-cost aluminum or brass craft wire. Craft wire comes in a wide variety of colors and sizes and costs much less than precious metal wire.
2. Choose box joint pliers. Box joints maintain the alignment of the pliers' jaws, even under stress.
3. Work directly from the spool. When using precious metal wire (after you've practiced on craft wire), work right off the spool of wire to avoid wasting any.
4. Protect your eyes. When snipping wire, hold your non-dominant hand over the blades to keep small pieces from flying toward your face.
5. Keep that sterling silver wire shining! Silver tarnishes from humidity in the air. To help keep your silver from tarnishing, keep your wire in plastic bags and add a small silica/desiccant package that often comes with new shoes and handbags.
6. Prevent nicks in your wire jewelry findings. To prevent nicks and mars on your wire, cover your metal-jawed pliers with bandage tape or dip them into a protective liquid plastic.
Iearn Jewelry Design Jewelry Desgin Sketches Ideas 2014 Neclkace Ring Earringes Gallery Bangles Software Drawing Images Photos Wallpapers
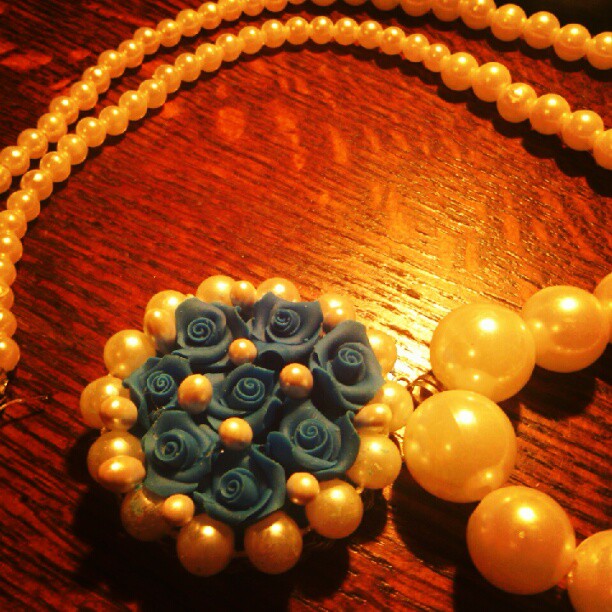
Iearn Jewelry Design Jewelry Desgin Sketches Ideas 2014 Neclkace Ring Earringes Gallery Bangles Software Drawing Images Photos Wallpapers

Iearn Jewelry Design Jewelry Desgin Sketches Ideas 2014 Neclkace Ring Earringes Gallery Bangles Software Drawing Images Photos Wallpapers

Iearn Jewelry Design Jewelry Desgin Sketches Ideas 2014 Neclkace Ring Earringes Gallery Bangles Software Drawing Images Photos Wallpapers

Iearn Jewelry Design Jewelry Desgin Sketches Ideas 2014 Neclkace Ring Earringes Gallery Bangles Software Drawing Images Photos Wallpapers

Iearn Jewelry Design Jewelry Desgin Sketches Ideas 2014 Neclkace Ring Earringes Gallery Bangles Software Drawing Images Photos Wallpapers

Iearn Jewelry Design Jewelry Desgin Sketches Ideas 2014 Neclkace Ring Earringes Gallery Bangles Software Drawing Images Photos Wallpapers

Iearn Jewelry Design Jewelry Desgin Sketches Ideas 2014 Neclkace Ring Earringes Gallery Bangles Software Drawing Images Photos Wallpapers

Iearn Jewelry Design Jewelry Desgin Sketches Ideas 2014 Neclkace Ring Earringes Gallery Bangles Software Drawing Images Photos Wallpapers

No comments:
Post a Comment